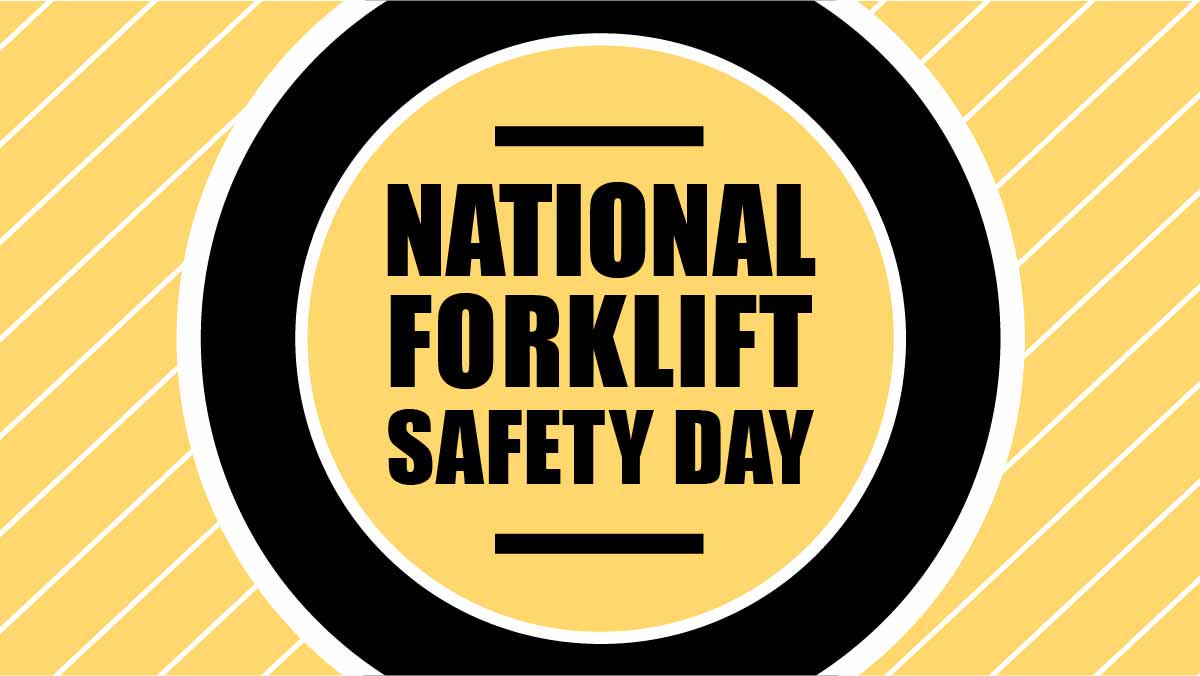
National Forklift Safety Day To Emphasize Operator Best Practices
Today marks the 7th annual National Forklift Safety Day, typically held in Washington DC. However, due to the challenges of COVID-19 this year, the event will be held as a virtual event.

The annual event serves as the focal point for forklift manufacturers to reinforce the importance of operator safety training and forklift safety practices. And, although it’s a virtual event this year, the format will remain the same with presentations from government representatives, safety experts and industry representatives. It’s an opportunity for the industry to unite behind safety and, perhaps this year more than ever, discuss and focus on the need to reinforce the need for operator best practices.
In fact, recently another company has been cited by the Occupational Safety and Health Administration (OSHA) in the USA after multiple hazards caused an employee to suffer fatal injuries. The United States Department of Labor Services says the employee was crushed by a forklift in September of 2019. OSHA has proposed more than USD52,000 in penalties after the portable restroom company was cited for nine violations. OSHA asserts the company failed to adequately train employees in using forklifts, amongst other safety violations.

The most common requirement of occupational health and safety entities throughout the world is the pre-shift forklift inspection; and for good reason. Pre-shift inspections are designed to be a proactive precaution to identify possible hazardous issues with forklifts and lower the risk of a forklift related injury or fatality.
With alarming levels of workplace injuries and deaths in the US and Canada related to forklifts, why aren’t more companies complying with the regulatory entities in North American and around the world and completing pre-shift inspections? While the evidence is somewhat anecdotal, companies report resistance having to do with not unformed habits due to lack of management-initiated processes, management resistance to the cost or not seeing enough value, and the process of using, keeping track of, and filing of paper reports.
In this digital world, and the age of “going green”, a solution to any inadequate arguments for not completing pre-shift inspections has now been eliminated.

The new MasterCheck app automates and simplifies the inspection process by providing operators with a quick and easy way to complete inspections from any type of device. The app remembers the operator and forklift information and quickly populates all identification fields. Operators then complete forklift inspections, repair reports, accident reports and near-miss reports, even including relevant photos, then simply click “send” to have the inspection sent to their supervisor and saved in the cloud. No more looking for lost paper reports – everything is automated.
The operator’s app is synced to the company’s web-based Supervisor Dashboard and provides the supervisor with important operational analytics and management tools including Pass/Fail history sorted by operator or forklift and accident, near miss and repair report graphs full of important data. From the Supervisor Dashboard the supervisor can also set up custom notifications to anyone else in the company regarding any type of occurrence.
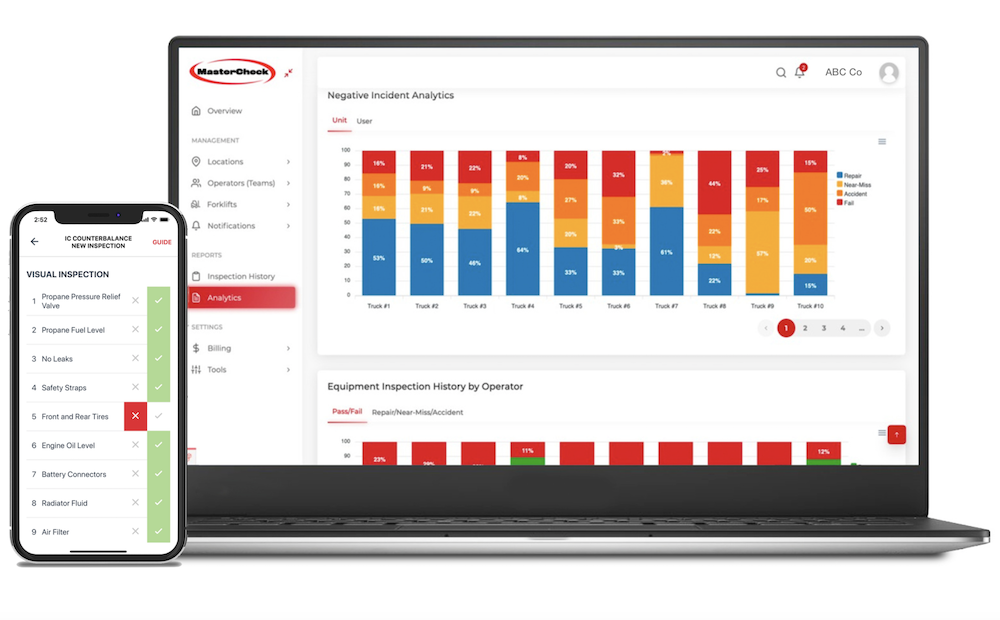
Want to add or edit any safety item on a specific inspection? The supervisor can customize inspection forms to suit the company’s specific requirements and the changes will instantly appear on the operators app.
Users of the MasterCheck app with web-based Supervisor Dashboard agree that it remedies any resistance to completing the important pre-shift inspections, while providing insights not available to management before, making the workplace an even safer one.
“We use the MasterCheck forklift inspection app for thirty-five forklifts in our locations throughout North Carolina and Texas, and it’s saving us a tremendous amount of time and paperwork,” said Glen Wegel, VP Operations, Kitchen Cabinet Distributors.
Sorry, the comment form is closed at this time.